Table of Contents
Subscribe Now
Whatsapp: + 1- 626 734 5510
Email: info@wingtubag.comHow to Choose a Reliable Handbag Manufacturer: 5 Red Flags to Avoid
Choosing a handbag manufacturer is key to brand development. Whether it is creating a high-end brand or building a sustainable fashion business, the choice of manufacturer is crucial. Inappropriate factory cooperation may lead to delivery delays, quality instability and other problems, affecting the brand image.
As a company with 12 years of experience in handbag manufacturing, we have served many international brands and are well aware of the common mistakes that companies make when choosing a manufacturer. Below we will share some important evaluation criteria to help you build a strong and reliable relationship.
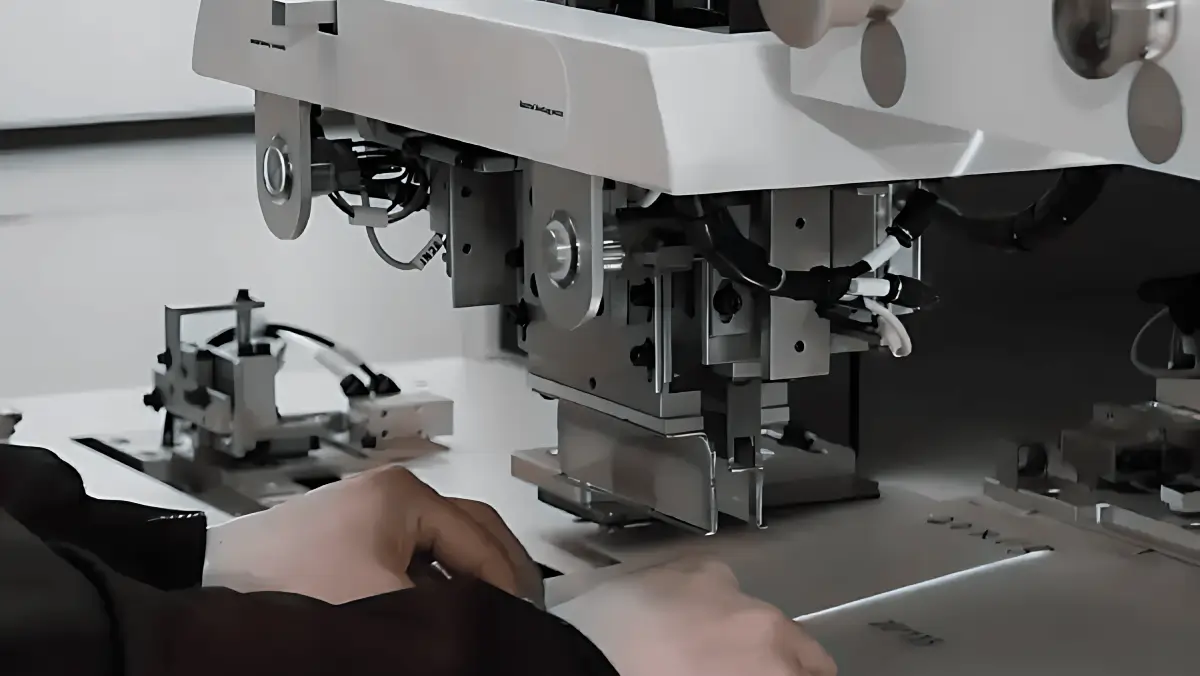
Red Flag 1: Vague Communication & Hidden Costs
If a factory hesitates to answer direct questions about materials, MOQs (Minimum Order Quantities), or pricing breakdowns, it’s a red flag. Vague replies such as “Don’t worry, we’ll handle it” often mask hidden fees like mold charges or sampling delays.
Real-World Risk:
One of our clients once paid 30% extra for “unexpected leather treatment fees” with a previous supplier.
Our Solution:
At Wingtubag, we provide transparent cost breakdowns upfront, including:
- Material options (genuine leather, recycled fabrics, etc.) with price tiers.
- Detailed MOQ flexibility (as low as 100 units for private label orders).
- Free 3D renderings before prototyping.
Red Flag 2: No Certifications or Ethical Audits
Factories lacking ISO 9001, SEDEX, or OEKO-TEX certifications may cut corners on labor rights or environmental compliance, risking your brand’s alignment with EU/US regulations such as California’s Supply Chain Act.
Did You Know?
67% of consumers will boycott brands linked to unethical manufacturing (Source: McKinsey 2023).
Our proud commitment holds
Red Flag 3: Limited Customization & Rigid Processes
Some manufacturers offer only “catalog copies” with no CAD/CAM support, forcing brands to compromise on design originality.
Client Story:
A startup wanted to combine vegan leather with upcycled denim accents but was told, “Our machines can’t handle mixed materials.”
Our Capabilities:
From sketch to shelf, we empower creativity with:
- 3-5 Day Rapid Prototyping: Modify hardware, stitching, or dimensions effortlessly.
- Hybrid Material Expertise: Mix fabrics, metals, and even biodegradable trims.
- Real-Time Order Tracking: Monitor production via our client portal.
Red Flag 4: Inconsistent Quality Control (QC)
Without a rigorous QC system, defects like uneven stitching or faulty zippers can slip through, leading to costly returns.
Industry Insight:
A 2022 study found that 23% of fashion brands lose over $50k annually due to QC failures.
Our 6-Step QC Process:
- Raw material inspection.
- Mid-production spot checks.
- Pre-shipment batch testing.
- AQL 2.5 standard compliance.
- Custom packaging validation.
- Door-to-door logistics insurance.
Red Flag 5: No References or Portfolio
A manufacturer refusing to share client references or portfolio samples likely lacks proven expertise.
Ask These Questions:
- “Can you show me bags similar to my design?”
- “Do you work with brands in my niche (e.g., luxury, eco-friendly)?”
Why Trust Us?
We’ve partnered with:
- Sustainable fashion brands for organic cotton tote bags.
- High-end retailers to deliver crocodile pattern clutches.
Your Next Step: Partner with Confidence
Choosing a manufacturer isn’t just about cost – it’s about shared values, transparency, and agility. At Wingtubag, we turn these principles into action. Contact us today to learn more about how we can support your brand’s success.